Date & Venue:
Friday, 18 October 2019
EF122
Abstract:
An atomic force microscope consists of three basic components: a microcantilever with a sharp probe at one end, an XYZ nanopositioner, and an optical beam deflection system to measure the tip deflection of the microcantilever due to interaction forces between the tip and sample. It is a versatile tool used to interrogate samples with atomic resolution.
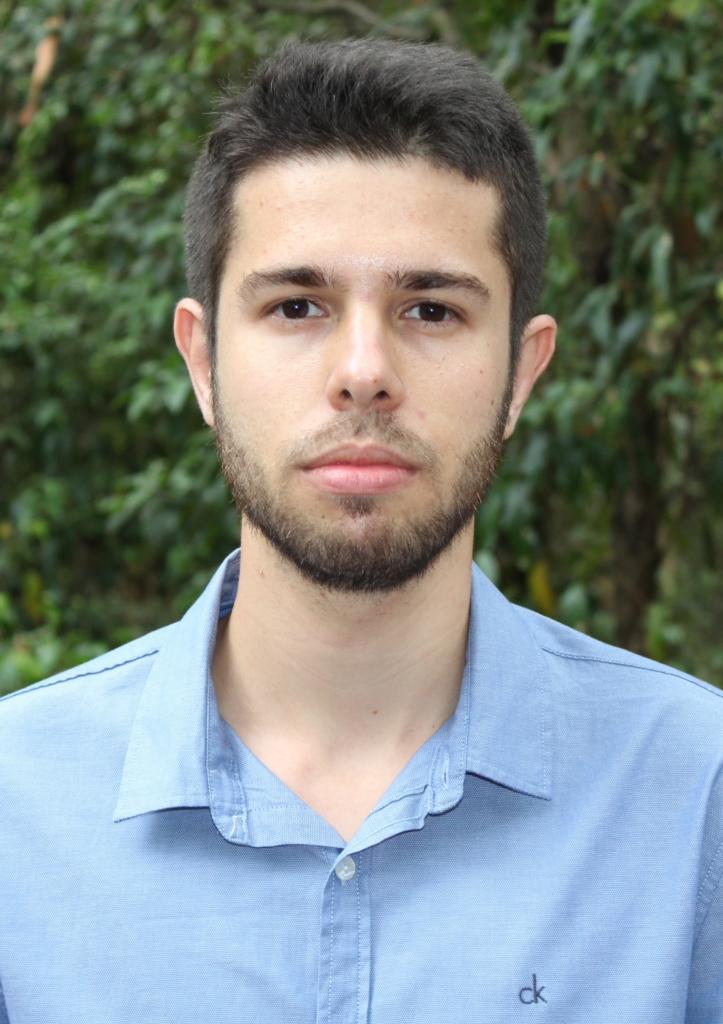
In dynamic AFM modes such as intermittent-contact mode, the cantilever is excited at its resonance frequency using a piezoelectric actuator embedded in the microscope structure. However, when observing the cantilever deflection, the resonance modes of both the cantilever and microscope structure are present. This complicates the identification of the desired cantilever resonance mode, which may be buried in hundreds of structural modes. The proposed research focusses on an alternative method where the actuator is integrated into the cantilever itself which eliminates the excitation of additional resonance modes. This approach dramatically simplifies the operating of an AFM, especially in liquid environments where it may be difficult or impossible to differentiate cantilever and structural modes.
The proposed on-chip actuators can also be used for creating static deflection and controlling the tip-sample separation, rather than using the sample or probe scanner. This increases the vertical positioning bandwidth from hundreds of Hertz to tens of kilohertz. These improvements can be used to increase the imaging speed of modes such as off-resonance tapping by a similar factor, i.e. potentially ten to one-hundred times.
A third issue with AFM performance is the optical beam deflection system which has a measurement spot size of approximately 10um. That is, the cantilever width must be at least 10um, which is undesirable since the width is proportional to stiffness and consequently, sample damage during imaging. Current optical deflection sensors also require tedious alignment of the laser, cantilever, and photodiode. To address these issues, this research proposes piezoelectric sensors integrated into the cantilever. This approach is compatible with further miniaturization and eliminates the need for an optical deflection system. However, when integrating sensing and actuation, a new issue arises as the sensor is no longer able to differentiate between the displacement induced by the piezoelectric actuator and tip-sample interaction forces.
This research aims to develop a novel microcantilever with integrated dual sensing for atomic force microscopy with application to off-resonance tapping mode. The proposed system is able to measure tip force and displacement simultaneously. These measurements allow the force to be controlled at each tapping point, making it possible to generate high-speed force-distance curves at each pixel of interest. The design process is performed by analytical modeling of a rectangular cantilever probe, which is confirmed with finite element analysis. To date, the design and manufacture of four microcantilevers is complete. Future work includes characterisation and control of the cantilevers, and geometric optimisation for the applications of interest.
Speaker Biography:
Natã Franco received a Bachelor in Control and Automation
Engineering by The Federal Center for Technological Education of Minas Gerais (CEFET/MG), in Brazil. His PhD is in Electrical Engineering for the Precision Mechatronics Lab, at The University of Newcastle. His research interests include mechanical design, applied control and modeling of linear systems.